shopVOX Pro
Getting started with shopVOX Pro
What is shopVOX? - shopVOX Pro
Getting started with shopVOX - shopVOX Pro
Your Account - shopVOX Pro
Icons and Interface Tour - shopVOX Pro
Inviting Users to Your Team - shopVOX Pro
Setting Roles for your Team - shopVOX Pro
My Profile + SMTP Settings - shopVOX Pro
Import Customers & Contacts from your Accounting software - shopVOX Pro
Adding Vendors - shopVOX Pro
How do I Update Our Billing Info? - shopVOX Pro
Setup Vendor Catalogs - shopVOX Pro
A Guide to Creating Your First Order - shopVOX Pro
Microsoft Outlook - Two Factor Authentication - shopVOX Pro
Customize your account with Add-on Features - shopVOX Pro
Importing and Exporting Customers & Contacts with a spreadsheet - shopVOX Pro
Transactions: New Quote + Quote Approval Process - shopVOX Pro
Database Migration Support for shopVOX - Legacy data - shopVOX Pro
Notifications: Keep your entire team up to date - shopVOX Pro
Color Picker - Saving Colors - shopVOX Pro
Transactions: What are Transactions? - shopVOX Pro
Transactions: New Sales Order - shopVOX Pro
"What's New" Feature: Your Guide to shopVOX Updates - shopVOX Pro
How Do I Cancel My shopVOX Account? - shopVOX Pro
Transactions: New Invoice - shopVOX Pro
How to Create a Quote - shopVOX Pro
shopVOX's History Tracking for Quotes, Sales Orders, Invoices, and Jobs - shopVOX Pro
Save Time with Emailed Document Templates - shopVOX Pro
Webinars in shopVOX Pro: Learn and Grow with Us - shopVOX Pro
shopVOX Express vs. Pro. Explaining the differences in Workflow - shopVOX Pro
Optimizing Quotation Efficiency: Unlocking the Power of Multiple Quantities with shopVOX - shopVOX Pro
Workflows - Quick Overview Express VS Pro - shopVOX Pro
Global Search in shopVOX - shopVOX Pro
Step Board: A Smarter Way to Track Jobs in Your Workflow - shopVOX Pro
Machine Scheduler - shopVOX Pro
Enhancing Security with Multi-Factor Authentication in shopVOX - shopVOX Pro
Installation Job Board - shopVOX Pro
Setting Up SMS using Twilio - shopVOX Pro
Sales - shopVOX Pro
Managing Customer and Leads
Workflow Stages and Templates Explained - shopVOX Pro
Using a TV for your Job Board - shopVOX Pro
Connecting shopVOX to QuickBooks Desktop: Streamlined Sync for Your Financials - shopVOX Pro
How to Price Color Changes - shopVOX Pro
Customer Alerts & Flags
Sales Commissions - shopVOX Pro
Creating Your Own Custom Job Views - shopVOX Pro
Updating a Workflow in shopVOX: A Complete Guide - shopVOX Pro
Streamline In-Store Payments with with Stripe Terminal or USB Credit Card readers - shopVOX Pro
Avalara AvaTax - Sales tax setup guide - shopVOX Pro
Merge Customers - shopVOX Pro
Adding new Contacts to Existing Customers - shopVOX Pro
Tracking Partially Fulfilled Apparel Orders in shopVOX
Customer Contacts: Setting Primary and Billing Contacts - shopVOX Pro
How to Price Color Matches - shopVOX Pro
Sales Leads on Business Intelligence Dashboard - shopVOX Pro
How to create Partial Invoices - shopVOX Pro
Multiple Currency Add-On - How it works and setting up - shopVOX Pro
Sales Leads - Sample Pipeline Setup - shopVOX Pro
Sales Order States - shopVOX Pro
Reports - shopVOX Pro
Understanding Quote Statuses in shopVOX - shopVOX Pro
Managing dates on Quotes, Sales Orders, and Invoices - shopVOX Pro
Products & Pricing - shopVOX Pro
Advanced Pricing concepts
Understanding Modifiers in shopVOX: Enhancing Product Pricing Flexibility - shopVOX Pro
Increasing Product Prices by a Percentage in shopVOX - PBase - shopVOX Pro
A Comprehensive Guide to Ternary Operations - shopVOX Pro
Using the Reference Field for Material Selection and Labor Charges - shopVOX Pro
Understanding Pricing Levels - shopVOX Pro
Mastering the Use of *, /, +, -, >, <, >=, <=, % in Ternary Operations - shopVOX Pro
How to Update Pricing in shopVOX: A Comprehensive Guide to Machine Rates, Labor Rates, and Materials - shopVOX Pro
Unlocking Efficiency: Harnessing System Variables and References to Create a Click Charge - shopVOX Pro
Undertanding Sell/Buy Ratio - shopVOX Pro
Product System Formula - with Filter - shopVOX Pro
Product Templates - Custom Formula Logic - shopVOX Pro
Product Template - Add New Defualt Items Configuration Window - shopVOX Pro
Workflow: Machine Time Formula
Custom Logic in shopVOX: Evaluating Multiple Boolean Modifiers - shopVOX Pro
Mastering the Use of &&, ||, and === in Ternary Operations - shopVOX Pro
Products: Utilizing the "Reference" Field to Combine two References into one Click Charge - shopVOX Pro
Golden Products
Golden Product: Flyer - with BOM - shopVOX Pro
Golden Product: Postcard- with BOM - shopVOX Pro
Golden Product: Greeting Cards - with BOM - shopVOX Pro
Golden Product: Calendar - with BOM - shopVOX Pro
Golden Products List by Global Region - shopVOX Pro
Products shopVOX Golden Products - shopVOX Pro
Golden Product: Brochures - with BOM - shopVOX Pro
Golden Product: Print + Copy - with BOM - shopVOX Pro
Golden Product: Business Cards - with BOM - shopVOX Pro
Golden Product: Booklet - with BOM - shopVOX Pro
Golden Product: Door Hangers - with BOM - shopVOX Pro
Adding Your Own Products - shopVOX Pro
How to Publish Products - shopVOX Pro
Product Templates & Formulas Explained - shopVOX Pro
Product Templates - Using System Formulas - shopVOX Pro
Product Templates - Using System Formulas - Adding a Double Sided check box - shopVOX Pro
Product Templates - User Created Formulas - shopVOX Pro
Product Templates - User Created Formulas - Adding a Double side check box - shopVOX Pro
Product Pricing - Round to 2 or 4 Decimal places - shopVOX Pro
Products: Grid Pricing Example - shopVOX Pro
Managing Your Product Catalog - shopVOX Pro
Setting Up Labor Rates in shopVOX: A Simple Guide - shopVOX Pro
Setting Up Machine Rates in shopVOX: A Comprehensive Guide - shopVOX Pro
Materials Management in shopVOX: A Comprehensive Guide - shopVOX Pro
Product Pricing: Material Wastage Calculator - shopVOX Pro
Product Features - Custom Fields - shopVOX Pro
Products - Pricing Type - Formulas - shopVOX Pro
Product Pricing : Cost Plus - shopVOX Pro
Uploading and Sending Proofs for Approval - shopVOX Pro
Product Templates - How to Turn on a Product Template - shopVOX Pro
Guide to Using the Panels UI - shopVOX Pro
How to Price Promotional Products - shopVOX Pro
How to Price Digitizing - shopVOX Pro
How to Price Direct To Garment Printing - shopVOX Pro
Product Template - Add New Drop-Down Menu Configuration Window - shopVOX Pro
Comprehensive Guide to Setting Up a Basic Apparel Product - shopVOX Pro
Pricing Methods: Standard, Product, and Cost Plus Pricing - shopVOX Pro
Custom Product, Template, and Code Modifiers - shopVOX Pro
Accounting and Reporting - shopVOX Pro
QuickBooks Desktop
Connecting Your Sage One Accounting - shopVOX Pro
Transaction Numbers Settings - shopVOX Pro
Add your Payment Gateway - shopVOX Pro
Connecting to your Accounting Software - shopVOX Pro
Connecting your XERO account - shopVOX Pro
Connecting Your QuickBooks Online Account - shopVOX Pro
Common Xero Sync Error messages explained - shopVOX Pro
Integrated SAGE Promo ( promotional catalog ) - shopVOX Pro
Setting Up Your Account - shopVOX Pro
Accounting
Common QB Questions - shopVOX Pro
Charging a Credit Card Fee - shopVOX Pro
Differences between USA QuickBooks Online and Non-USA QuickBooks Online - shopVOX Pro
shopVOX Setup of Tax Codes for Quickbooks Canada Desktop/Online - shopVOX Pro
How are Users Billed?
Five challenges to consider when setting up your Account - shopVOX Pro
How to Filter MFA Email Alerts in Outlook and Gmail - shopVOX Pro
shopVOX Work Flow - The Big Picture - shopVOX Pro
Leveraging External IP Addresses for Security - shopVOX Pro
Hide or Show Quotes & Sales Orders, Ordered Quotes, and Invoiced Quotes and Sales Orders - shopVOX Pro
Add Your Logo and Company Info - shopVOX Pro
How to add Additional Charges to your Quotes, Sales Orders and Invoices - shopVOX Pro
Terms and Conditions - shopVOX Pro
Document's and PDF Settings - shopVOX Pro
Group and Describe Jobs with Tags - shopVOX Pro
How to Change Password - shopVOX Pro
Forms: Customizing Forms - shopVOX Pro
Common Questions About Users - shopVOX Pro
Flagging a user as a "Sales Rep" - shopVOX Pro
Industry Specific Content - shopVOX Pro
Automation & Integrations - shopVOX Pro
Shipping
ShipStation integration - shopVOX Pro
Shipping Profiles - setting up Products to automate number of boxes - shopVOX Pro
APIs
What is an API? - shopVOX Pro
How an API Works: A Simple Explanation - shopVOX Pro
Leveraging the Power of shopVOX with API Integration - shopVOX Pro
API Essentials: Understanding the Backbone of Software Communication - shopVOX Pro
Building Your Own Custom Integration with shopVOX APIs - shopVOX Pro
JSON Demystified: The Universal Language of Data Exchange - shopVOX Pro
I'm having an issue with the shopVOX APIs. Who do I contact? - shopVOX Pro
Does shopVOX do custom development? - shopVOX Pro
Does shopVOX integrate with Salesforce? - shopVOX Pro
Setting up Mailchimp Integration - shopVOX Pro
Sales Leads Web Form in shopVOX: Streamline Prospect Capture and Management - shopVOX Pro
Simplify User Authentication with OAuth Integration in shopVOX
Who to Contact for shopVOX API Issues - shopVOX Pro
Setting up Constant Contact Integration in shopVOX
Does shopVOX integrate with Microsoft Project? - shopVOX Pro
API and Webhooks integration feature - shopVOX Pro
shopVOX Go! App - shopVOX Pro
Discovering Your shopVOX API Credentials: A Step-by-Step Guide - shopVOX Pro
Automation - Scheduled Actions - shopVOX Pro
What are some popular advantages when using Zapier? - shopVOX Pro
FAQs - shopVOX Pro
shopVOX specific terms
Common questions
How to increase Database size ? - shopVOX Pro
Opening PDFs directly in your browser - shopVOX Pro
shopVOX User Types - shopVOX Pro
Empowering Project Managers in the Proofing Process: A Guide to Workflow Enhancement - shopVOX Pro
Hex Color file to match PMS color chart - shopVOX Pro
How do I disabled user? - shopVOX Pro
What is the Admin checkbox for when creating a new user? - shopVOX Pro
Invoicing - Enhancing Customer Engagement: Tracking Invoice Views with shopVOX Pro
Where do jobs "fit" in the order process in ShopVOX? - shopVOX Pro
Why can't I print the PDF documents directly, instead of downloading? - shopVOX Pro
How can I send a quote and a proof together in one email to my customer? - shopVOX Pro
Terms and Definitions
Printing Examples - Letterpress Printing
Printing Types Defined
Printing Examples - Digital Printing
Printing Examples - Offset
Errors and Troubleshooting
How to clear history from Chrome browser?
When I convert a quote to a work order, does the name of the order and the line item description carry forward or do I have to rewrite?
How to optimize your browser for shopVOX - shopVOX Pro
Streamlining Proof Attachment to New Sales Orders for Enhanced Efficiency - shopVOX Pro
Setting Up Minimum Order Amounts in shopVOX - shopVOX Pro
What is our IP address for the mail server ? - shopVOX Pro
Custom PDF in shopVOX - shopVOX Pro
Onboarding - shopVOX Pro
Onboarding - Simple Products Setup
Mastering Product Setup in shopVOX: A Step-by-Step Guide from Basics to Advanced Customization - shopVOX Pro
Lesson 1: Setting Up a Basic Product - shopVOX Pro
Lesson 2: Introducing Dynamic Pricing Based on Square Footage - shopVOX Pro
Lesson 3: Enhancing the Product with Templates and Dropdown Menus - shopVOX Pro
Lesson 4: Adding a Default Item Linked to Modifiers - shopVOX Pro
Lesson 5: Implementing a Double-Sided Boolean Modifier with Conditional Logic - shopVOX Pro
Lesson 6: Replacing a System Formula with a Custom Formula - shopVOX Pro
Lesson 7: Integrating Custom Formula into the Conditional Double-Sided Logic - shopVOX Pro
Lesson 8: Adding an Additional Dropdown Menu - shopVOX Pro
Lesson 9: Creating Custom Fields to Enhance Usability - shopVOX Pro
Lesson 10: Implementing a Rush Charge Option - shopVOX Pro
Summary Conclusion: Lessons 1-10 - shopVOX Pro
Quoting and Order Management - shopVOX Pro
Adding/Updating Customers and Contacts - shopVOX Pro
Purchase Orders - How to Add Materials and Products to a Purchase Order in shopVOX PRO for the Inventory Add-on - shopVOX Pro
Stay Organized with Notes, Tasks, and Assets - shopVOX Pro
Roll-Up Line Items to Combine Pricing - shopVOX Pro
Purchasing and Receiving Blank Garments - shopVOX Pro
Creating Your Own Custom Views - shopVOX Pro
How to Issue Refunds and Credit Memos - shopVOX Pro
Add Ons - shopVOX Pro
Ecommerce
Ecommerce - Web Store - shopVOX Pro
Ecommerce: Creating Discount Codes - shopVOX Pro
Ecommerce - Steps to setup custom URL for paid cPortal - shopVOX Pro
Webstore & Shopping Cart Examples from shopVOX Users - shopVOX Pro
Setting up a Shopping Cart to sell online - Changing the URL - shopVOX Pro
Ecommerce - cPortal - White Label Setup - shopVOX Pro
Ecommerce - cPortal - shopVOX Pro
Ecommerce - Overview - shopVOX Pro
Empowering Your Customers with the Free cPortal - shopVOX Pro
Ecommerce - Shopping Cart - shopVOX Pro
Ecommerce - Apparel Web Store - shopVOX Pro
Inventory
Inventory Module Add-On - Setup and use of Feature - shopVOX Pro
Inventory Module Add-On - Setup Locations - shopVOX Pro
Questions to Consider About the Inventory Module in shopVOX - shopVOX Pro
Inventory Module Add-On - shopVOX Pro
Divisions
Vehicle Wrap
Amazon S3 Storage
Amazon S3 (Simple Storage Service) - Add-On - shopVOX Pro
Amazon S3 Add-On (Simple Storage Service) - Amazon S3 Pricing - shopVOX Pro
Amazon S3 Add-On (Simple Storage Service) - What is it? - shopVOX Pro
Projects in shopVOX: Comprehensive Guide - shopVOX Pro
Service Job Add-On: Streamline Your Workflow with shopVOX's New Service Job Feature - shopVOX Pro
Whats New
2025 Whats New
Thu, 02/27/2025 Update: Down payment can now be a dollar amount. Pro & Express
Fri, 01/24/2025 New Notification event: Job step Completed Pro
Wed, 01/29/2025 Highlight: Panel Pricing UI Pro
Sun, 01/19/2025 Freight charges on Purchase Orders Pro
2024 Whats New
Mon, 10/07/2024 Enhancement in Task Pro & Express
Thu, 05/16/2024 Quick Tip: Ability to copy Material/Product Names in Purchase Order Line Items Pro
Tue, 10/08/2024 New feature added: Task templates to prefill repeated Tasks Pro & Express
Tue, 09/24/2024 New update! Connect to your ShipStation account! Pro
Wed, 08/07/2024 Enhancing Dropdown Menus for Material Search Pro
Mon, 04/29/2024 Added a new link directly on the Home screen to navigate Reports
Mon, 07/29/2024 Ability to enter Ft and Inches vs just Inches. Pro
Wed, 06/05/2024 Added a new addition to the Products called 'Published'. Pro & Express
Mon, 04/22/2024 Option to conceal Costs and Markup for apparel items when adding line items
Sun, 10/27/2024 Role-Based Permissions for Editing or Overriding Line Item Costs(Unit Cost) Pro
Wed, 11/27/2024 Apparel images on customer PDF? Show or Don't show! Pro
Fri, 10/04/2024 New Apparel catalog available for US/CAN accounts! Pro & Express
Tue, 05/21/2024 Added New Email Template Tag: {{txn_downpayment}} Pro & Express
Wed, 05/01/2024 Daily Tip - Add shopVOX email id's as contacts!
Tue, 11/26/2024 Track Partially Fulfilled Apparel items on a Sales Order. Pro
Thu, 11/14/2024 We added a new valuable Update in Pricing templates! Pro
Wed, 05/15/2024 Enhanced Notification System: In-app Alert for Proof Uploaded Pro & Express
Wed, 07/24/2024 S3 Storage for your assets. Pro
Tue, 07/02/2024 Implemented the "Board Feet" Formula within the shopVOX Product System. Pro
Sat, 08/10/2024 Australia/New Zealand regional Golden Products have been updated! Pro & Express
Mon, 04/15/2024 Ability to import payments from Xero to shopVOX
Wed, 06/05/2024 Tasks, notes, and assets associated with a quote to sales order to invoice will now be displayed in the Related Assets section. Pro & Express
Thu, 05/09/2024 Dynamic Customer Identification in PDFs
Fri, 05/17/2024 Job Board Overview and Best Practices Pro & Express
Tue, 11/05/2024 2FA - Two Factor Authentication is now active (Optional) Pro & Express
Tue, 10/29/2024 Enhancement to the online proofing feature. Pro & Express
Fri, 07/19/2024 Included in the reporting are two new reports: 1. Quotes with Line Items, and 2. Sales Orders with Line Items. Pro
Thu, 08/08/2024 Microsoft Outlook - Two Factor Authentication Pro & Express
Wed, 05/15/2024 Avalara enabled Stores Changed the way of tax syncing to QBO
Fri, 01/24/2025 Highlighted feature: Quote Review and online approval Pro
Fri, 09/06/2024 Allow Line Item Taxable Override Pro & Express
Fri, 05/31/2024 Added another PDF for Invoice Statements: Aging Summary PDF. Pro & Express
Tue, 08/20/2024 Pro tip: Controlling and protecting access to your customer and transaction data! Pro
Mon, 10/28/2024 New Permission setting! Pro
Fri, 10/18/2024 eCommerce feature update: There have been recent Apparel Webstore improvements Pro
Wed, 10/16/2024 Announcement: Another new US Apparel catalog available! Pro & Express
Thu, 05/30/2024 “Mastering Customer Proof Reviews: Unveiling the Dollar Value Flag” Feel free to use or modify it as needed! 😊📝 Pro & Express
Wed, 11/06/2024 Colors: there is a new way to save colors! Pro & Express
Mon, 09/16/2024 Express & Pro webinar articles Pro & Express
Wed, 08/28/2024 Update: The Purchase Order State will automatically change from Draft to Ordered once the Vendor Order ID is eneterd on the PO. Pro & Express
Thu, 04/25/2024 Added Missing Email PDF types in SO level while sending emails
Thu, 05/02/2024 Quick Tip: Within each user profile, there's a setting to toggle between Full Screen Mode and Fixed Layout.
Fri, 11/08/2024 Download option for AI Template and PDF Template for Vehicle Wrap Products Pro
Tue, 07/02/2024 Introducing the "Total_Area" Formula in ShopVOX! Pro
Fri, 07/26/2024 Update: New option for measurements on a Product. Now you can enter Feet and Inches, instead of just Inches. Pro
Fri, 05/31/2024 Quick Tip: What does the yellow color indicate on a job board? Pro & Express
Mon, 02/10/2025 Ability to change the workflow on a job without deleting the job Pro
Mon, 04/22/2024 Added the JB# in all the Job related reports
Tue, 06/04/2024 Added Fulfilment Type Column on the Order Board. Pro
Thu, 04/25/2024 Ability to handle Spl charges like setup/shipping/Misc/finance charges through SO API
Fri, 02/28/2025 Payment Gateway link: Ability to turn the flag off by default when emailing customer Pro
Thu, 10/17/2024 Enhancements in Materials: Upload the Material Pictures on the Show Overview Only Screen. Pro
Mon, 09/09/2024 Restrict Users to add/change the Discounts on the Line Item of the Transactions Pro
Tue, 04/23/2024 Ability to add "external name" field on the labor rates.
Thu, 04/25/2024 Added functionality to restrict the users with IP addresses
Fri, 07/26/2024 Added Hide Ordered Client Orders flag under Transaction Settings. Pro
Tue, 10/22/2024 Send iCal Email for Service Jobs in Tasks section Pro
Wed, 08/28/2024 Enhancement in New Customer page Pro & Express
Mon, 05/13/2024 Disabled Adding custom line item to Non Admin Users
shopVOX Express
Getting Started with Express
Getting Started Checklist - shopVOX Express
A Guide to Creating Your First Order - shopVOX Express
shopVOX Overview - shopVOX Express
Icons and Interface Tour - shopVOX Express
How Do I Cancel My shopVOX Account? - shopVOX Express
How do I Update Our Billing Info? - shopVOX Express
Color Picker - Saving Colors - shopVOX Express
Enhancing Security with Multi-Factor Authentication in shopVOX Express
Syncing Job Line item names, on the Jobs Board - shopVOX Express
Webinars in shopVOX Express: Learn and Grow with Us - shopVOX Express
Setting Up Your Account - shopVOX Express
Accounting - shopVOX Express
Connecting to your Accounting Software - shopVOX Express
Connecting Your QuickBooks Online account to shopVOX Express
Quickbooks Online: Common Sync Errors - shopVOX Express
Connecting your XERO account to shopVOX - shopVOX Express
XERO accounting FAQs - shopVOX Express
Importing Your Customers and Contacts - shopVOX Express
Add your Payment Gateway - shopVOX Express
Inviting Users to Your Team - shopVOX Express
Add Your Logo and Company Info - shopVOX Express
Group and Describe Jobs with Tags - shopVOX Express
Connecting Your Sage One Account to shopVOX - shopVOX Express
Setting Roles for your Team - shopVOX Express
SMTP Settings - shopVOX Express
Created Canned Message Templates for Your Team to Use - shopVOX Express
Adding Vendors - shopVOX Express
Quote and Order Management - shopVOX Express
Adding/Updating Customers and Contacts - shopVOX Express
How to Issue Refunds and Credit Memos - shopVOX Express
Stay Organized with Notes, Tasks, and Assets - shopVOX Express
Purchasing and Receiving Blank Garments - shopVOX Express
Creating Your Own Custom Views - shopVOX Express
Roll Up Line Items to Combine Pricing - shopVOX Express
Give customer options using No total Pdf - shopVOX Express
Invoice statements: creating and sending to a customer - shopVOX Express
Production Management - shopVOX Express
Track Progress with Job Statuses - shopVOX Express
Managing Job Statuses and Deadlines - shopVOX Express
Creating Jobs for Tracking Production - shopVOX Express
Using a TV for your Job Board - shopVOX Express
Creating Your Own Custom Job Views - shopVOX Express
Uploading and Sending Proofs for Approval - shopVOX Express
Products and Pricing - shopVOX Express
Golden Product - shopVOX Express
Golden Products - Booklet - with BOM - shopVOX Express
Golden Products - Business Cards - with BOM - shopVOX Express
Apparel Decoration - shopVOX Express
How to Price Graphic Design (for apparel decorators) - shopVOX Express
How to Price Screen Printing - shopVOX Express
How to Price Promotional Products - shopVOX Express
Setup pricing for blank apparel with our Vendor Catalogs - shopVOX Express
How to Price Digitizing - shopVOX Express
How to Price Color Matches - shopVOX Express
How to price apparel with Mixed Decoration - shopVOX Express
How to Price Color Changes - shopVOX Express
Integrated SAGE promotional catalog - shopVOX Express
How to price Direct To Garment printing - shopVOX Express
What are Products? - shopVOX Express
Guide to apparel decoration pricing - shopVOX Express
Setting Your Shop Hourly Rate - shopVOX Express
Adding Your Own Products - shopVOX Express
Customizing the Base Products - shopVOX Express
**Golden Products List by Global Region - shopVOX Express
Golden products - Our pre-made pricing templates and new versions - shopVOX Express
- All Categories
- shopVOX Pro
- Add Ons - shopVOX Pro
- Inventory
- Inventory Module Add-On - Setup and use of Feature - shopVOX Pro
Inventory Module Add-On - Setup and use of Feature - shopVOX Pro
Updated
by Tyler MacDonald
This feature is typically utilized by customers with pre-made products stocked for quick turnaround, especially prevalent among high-volume apparel businesses seeking control over quantities. To determine whether Inventory is a suitable fit for your shop, refer to this informative article.
How to Best Use This Guide:
This comprehensive guide focuses on setting up the Inventory feature in your shopVOX Pro account. It is strongly recommended to read through the entire article from start to finish for a thorough understanding.
Tracking Materials vs Products:
In the context of shopVOX:
- Materials: Refers to raw goods used in the manufacturing or creation of a finished product, such as vinyl media, substrate material, blank apparel, or paper/card stock.
- Products: Encompasses finished retail items where no further modifications are made. The application of a markup to wholesale goods is the primary action.
Your first decision is whether you'll be tracking Materials or Products. Most users, especially those in custom shops, will track inventory on Materials—the physical components (raw goods) purchased to create the end product sold to customers.
However, if you operate a retail shop or sell retail products, where you acquire finished items from vendors, mark them up, and then resell them, tracking Product inventory is essential. Given that these completed items are ready to sell, the Inventory add-on facilitates effective tracking. It's worth noting that you can track both Materials and Products within the same account if your business involves selling both types of items.
Optimal Use for Your Industry: Custom Shop
If your business falls into categories such as Sign, Screen Printing, Embroidery, Awards, Print, or any other custom manufacturing shop, it is advisable to track inventory on Materials rather than Products. The rationale behind this recommendation is rooted in the fact that, in your industry, the end Product is something you create. Instead of purchasing a final Product from vendors, you acquire raw materials and use them to craft the end Product.
Industry-specific Examples:
- Sign Industry: Materials encompass substrates, vinyl, lamination, inks, grommets, etc.
- Print Industry: Materials include cardstock, paper, inks, and similar components.
- Awards & Engraving Industry: Raw components like plaque boards, sheet plastic/metal, trophy columns/figures/hardware, and even engraveable items such as acrylic/glass/crystal awards are considered Materials. In this context, you don't stock engraved products; rather, you maintain inventory of blank awards (Materials).
- Screen Printing/Embroidery: In the case of apparel-related businesses, a blank T-shirt is commonly referred to as a Product. However, within shopVOX, a blank T-shirt is categorized as a "Material" because it serves as the foundation for producing the finished Product—a screen-printed T-shirt.
- Custom Manufacturing: Materials may consist of metal, wood, or plastic parts that come together to create a distinctive custom finished product.
By aligning your inventory tracking with Materials, you ensure a more accurate reflection of your unique manufacturing process in a custom shop setting.
Retail Shop:
For retail businesses, it is advisable to track inventory on Products, especially when dealing with retail products marked up for sale.
Key Tracking Features:
Within the Inventory feature, you have the ability to monitor two critical aspects related to the items you select:
- Inventory Levels:
- This denotes the quantity of each item in your possession, commonly referred to as inventory counts.
- Inventory by Location:
- This involves tracking the quantity of each item along with their respective locations. While optional, the capability to track the physical locations of your items can be valuable. This is particularly useful if your business operates across multiple warehouses or sections, contributing to the maintenance of accurate and well-organized records.
How to Set Up Inventory Tracking
Step 1: Enable Inventory Tracking
After determining the materials or products you intend to track inventory for, proceed to the Product or Material settings. Locate and select the option "Track Inventory," as illustrated in the image below. Check the corresponding box to activate inventory tracking for the chosen items.
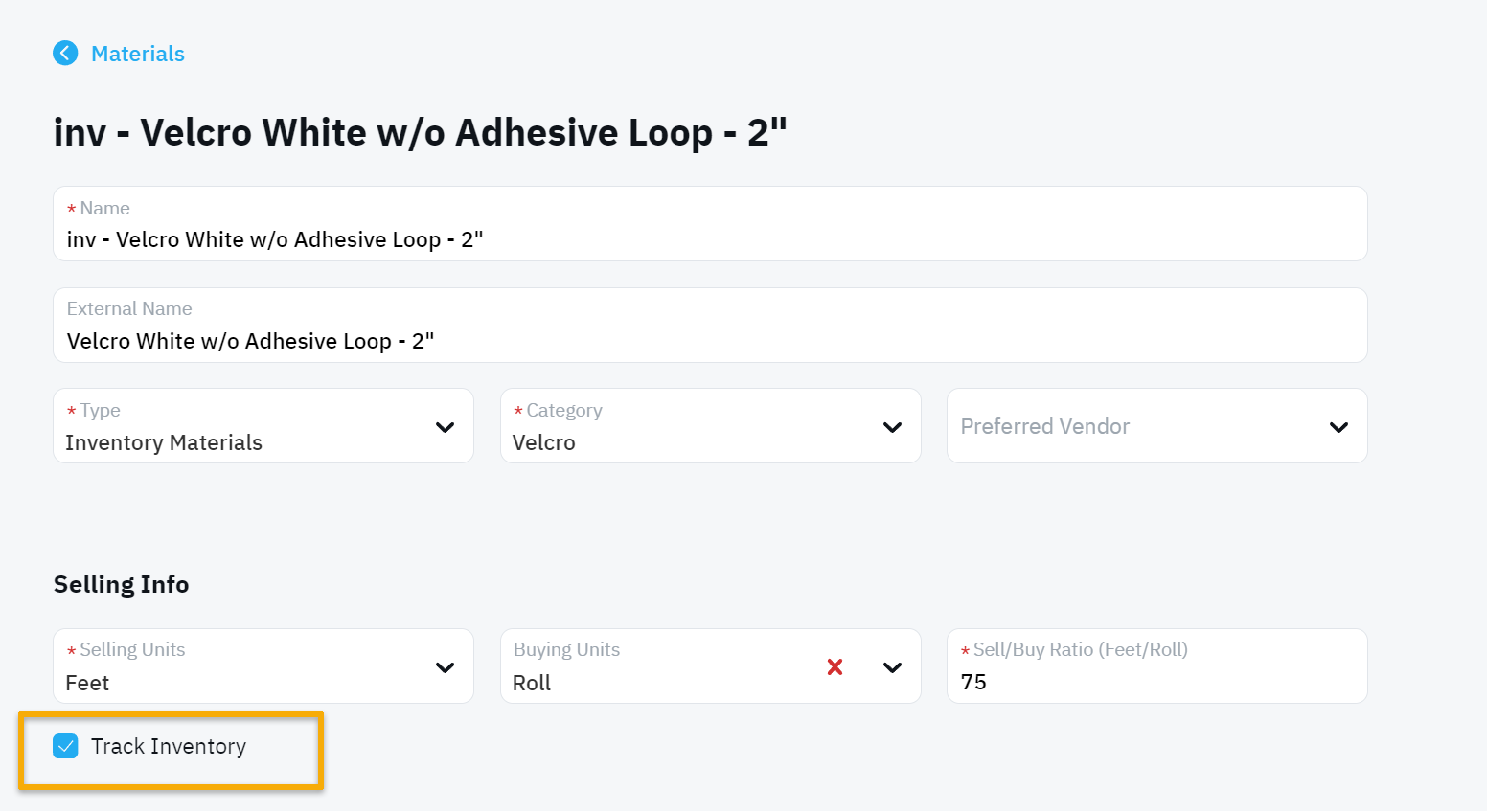
IMPORTANT NOTE:
- Sell/Buy Ratio Setup: Ensure the correct configuration of the "Sell/Buy ratio," especially if you are using different Units of Measurement (UOM) for Selling and Buying Units.
- Visibility of "Track Inventory" Flag: If the "Track Inventory" flag is not visible, navigate to Account Settings > Forms. In this section, make sure to check the "Track Inventory" checkbox in either the Materials Forms and/or the Products Forms settings. This step is essential for the proper display of the "Track Inventory" flag.
Step 2: Enter Inventory Quantity
To effectively track inventory, access each Material or Product you've chosen to monitor and enter the current Quantity on Hand (shown below).
Materials:
If you are tracking Materials, you will find the Inventory details positioned below the Material details. Enter the accurate Quantity on Hand for each Material to initiate precise inventory tracking.
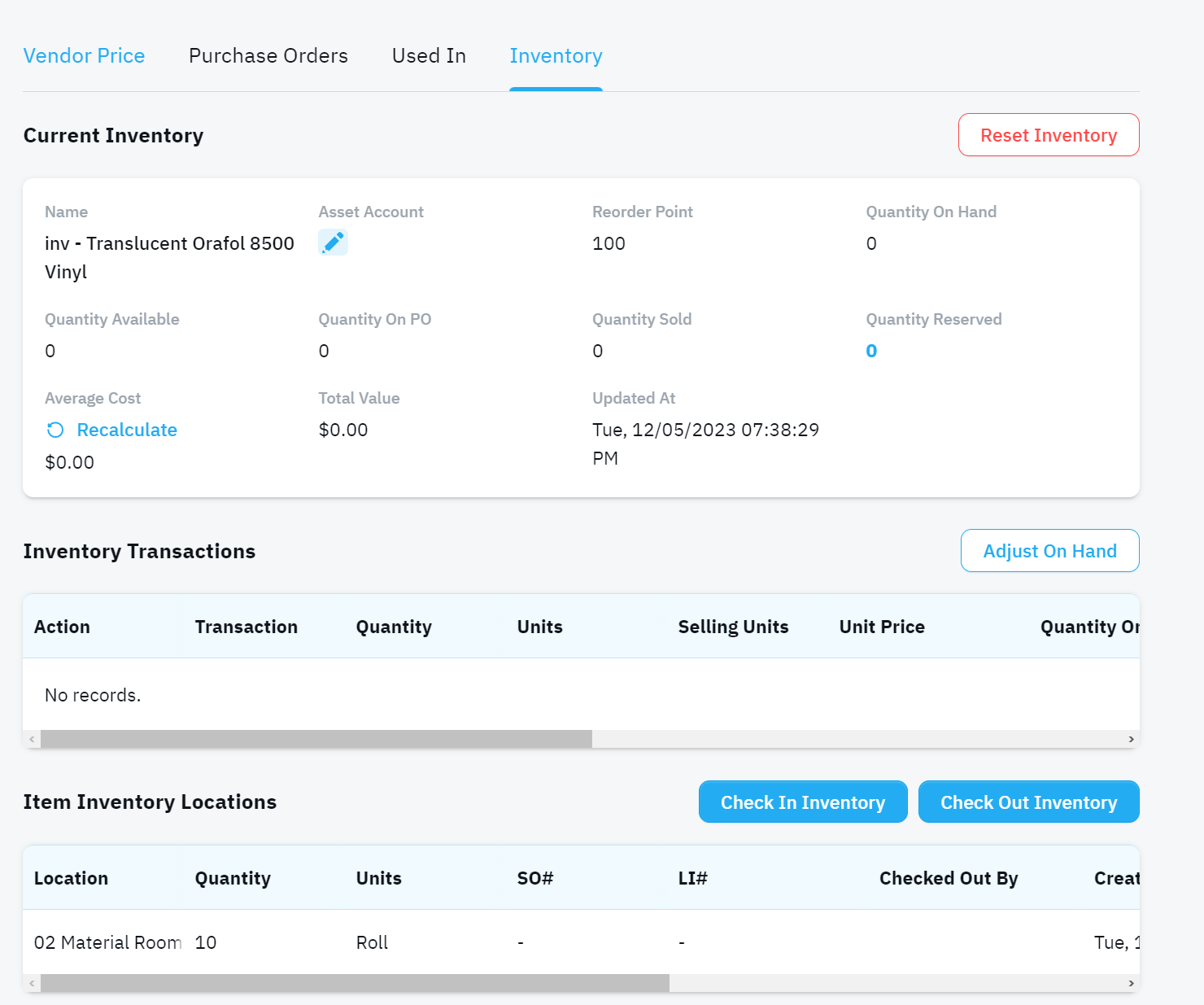
Products:
For those tracking Products, locate the Inventory details within the "Inventory" tab available in the left-hand side menu. Click on the link to open the Inventory details page, where you can input and manage the Quantity on Hand for each Product. This step ensures accurate and efficient tracking of inventory for your selected Products.
Ensure accuracy in all other details for each Material/Product. An explanation of the meaning of each field is provided below:
Field Definitions:
The following is a comprehensive list of all Inventory Fields and their definitions:
- Reorder Point:
- This is the threshold quantity that, when reached, signals that the Material/Product should be reordered to maintain sufficient stock levels.
- Qty on Hand:
- The total quantity of the Material/Product available on hand, inclusive of quantities on Sales Orders.
- Calculation: Qty on Hand = Qty Available + Qty Reserved
- The total quantity of the Material/Product available on hand, inclusive of quantities on Sales Orders.
- Qty Available:
- The quantity of the Material/Product that is available for new orders.
- Qty On PO (Purchase Order):
- The quantity presently listed on an outstanding 'Open' Purchase Order that has not yet been "Received."
- Qty Sold:
- The cumulative total quantity sold since the inception of tracking.
- Qty Reserved:
- The quantity "Reserved" for other Open Sales Orders (SO). These quantities are consumed upon the completion of an open SO. If the SO is voided, the Qty Available increases, and Qty Reserved decreases.
- Avg. Cost (Average Cost):
- The average cost of the Products/Materials based on quantities on hand.
- Total Value:
- The total monetary cost of the quantities on hand.
How shopVOX Updates Inventory Levels:
Once inventory tracking has been enabled for a specific Product/Material in shopVOX, there are three ways in which the system updates inventory counts/levels:
- Auto Update:
- Unlike the other two methods, Auto Update can be toggled on or off for your entire account. When activated, the system automatically updates inventory counts whenever there is any transaction impacting inventory. To enable Auto Update, navigate to the Setting/Transactions, and toggle Auto Update Inventory on/off
- Unlike the other two methods, Auto Update can be toggled on or off for your entire account. When activated, the system automatically updates inventory counts whenever there is any transaction impacting inventory. To enable Auto Update, navigate to the Setting/Transactions, and toggle Auto Update Inventory on/off
- Manual Update:
Inventory can be manually updated within the following transactions:
- Sales Orders
- Invoices
- Purchase Orders
- Material Receipts
After completing a transaction (with no additional changes to be made), navigate to the blue actions menu and select the "Update Inventory" option.
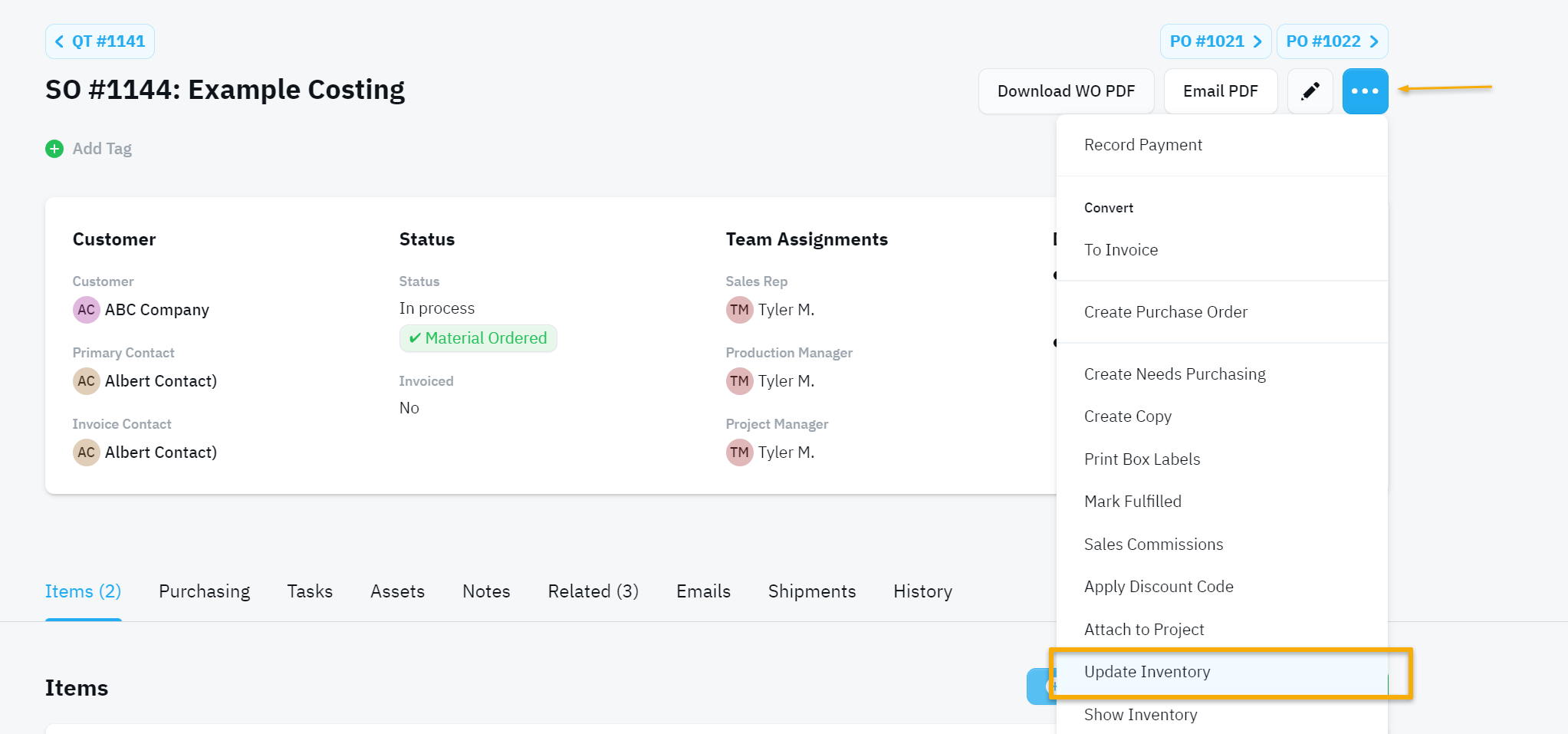
When you click "Update Inventory," products or materials set to "track inventory" will be adjusted based on the ongoing transaction. This functionality is always active and doesn't require activation. However, it necessitates manual initiation by clicking the button before inventory is actually updated from the mentioned transactions.
Why use manual update? In scenarios where multiple changes may occur during the Sales Order process before finalization, the manual update feature allows you to decide when to update the inventory, providing flexibility and control over the process.
- Manual Adjustments:
Manual adjustments allow you to manually "check in" or "check out" inventory from one physical location to another, referred to as transactions. Further details on this option can be found in the final section of this article.
Additionally, you can perform a manual adjustment to the Quantity on Hand within the Material or Product settings. Simply select "Adjust on Hand."
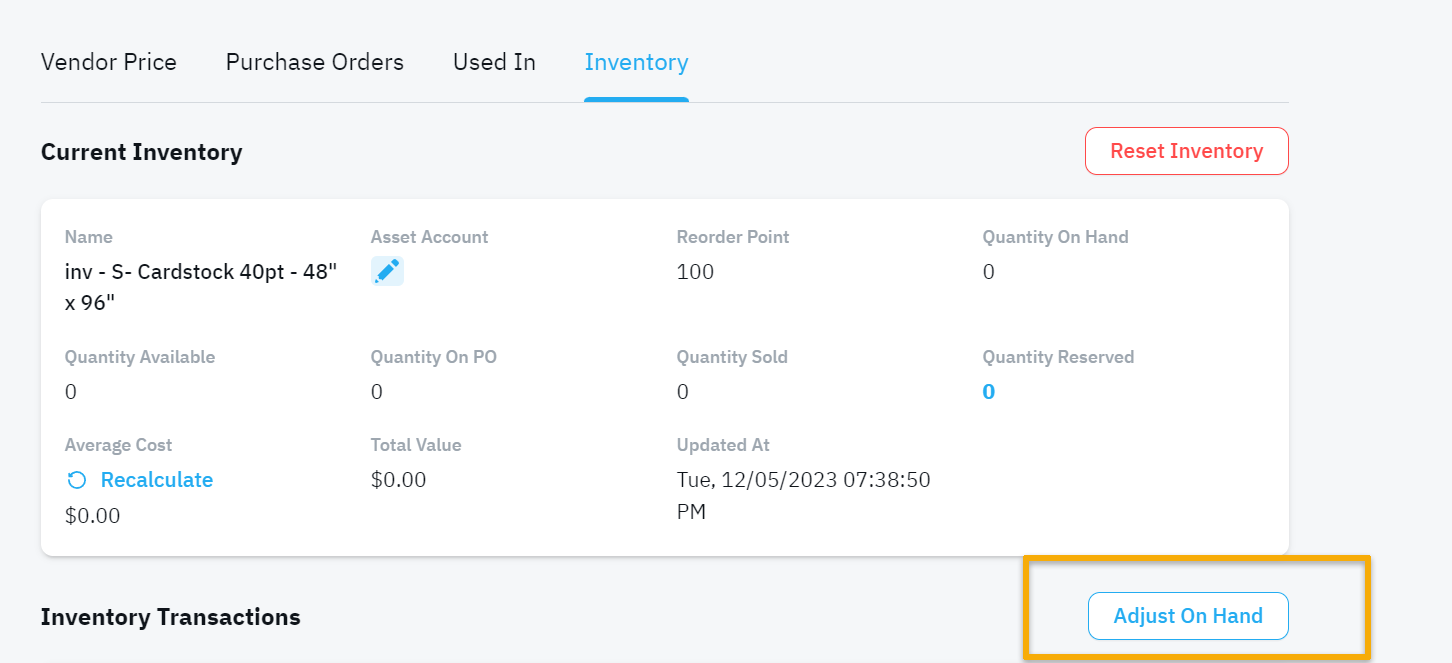
You can then make additions or subtractions to the "Quantity on Hand" as needed. This feature provides a direct method for precise adjustments to inventory levels based on your specific requirements.
You can then make an addition or subtraction to the "Quantity on Hand".
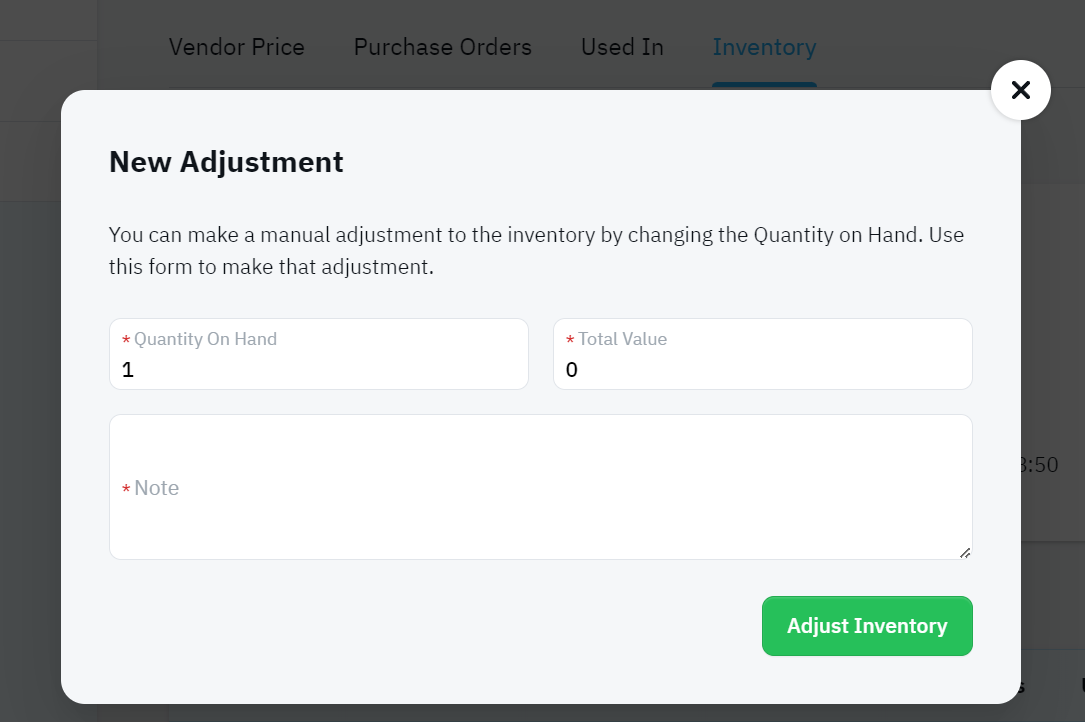
